Key Considerations and Solutions in Automation Equipment Design: Path to Efficiency and Precision Improvement
Introduction
■ Design Objective (Why the equipment is needed)
When starting the design of an automation system, the most critical step is to clearly define why the equipment is necessary and what specific purpose it will serve. The decision to introduce new equipment typically arises from challenges or problems in existing processes. This section examines the issues that have arisen in current processes and analyzes how the equipment can solve these problems.
・Problems in Existing Processes
Many factories and production lines still rely on manual or semi-automated processes, often leading to the following issues:
- Increasing labor costs: Manual processes directly tie to labor costs, which can significantly increase overall costs. In high-volume production, it becomes difficult to maintain a high output with a small workforce.
- Inconsistent quality: Manual tasks often result in variations in quality, influenced by the worker's experience, physical condition, or individual skills, making it difficult to ensure uniform product quality.
- Production speed limitations: Human labor has its limits, so when production demands increase rapidly, it becomes challenging to keep up. Quick responses are particularly needed in markets with fluctuating demand.
- Worker fatigue: Repetitive and physically demanding tasks can increase the burden on workers, leading to long-term health risks or accumulated fatigue.
・Current Process Analysis
A thorough analysis of the current workflow and processes is the first step toward appropriate automation design. For instance, identifying which tasks consume the most time, where errors or mistakes are most likely to occur, or which processes act as bottlenecks are essential. This information is vital for determining where automation can be most effective.
By conducting interviews and collecting data from the field, it’s possible to visualize the workflow and uncover the core issues. For example, if material supply is delayed at a particular step, it could be causing a delay in the entire process. Such problems may be solvable through automation.
Design Goals (What would the ideal equipment look like?)
Clearly defining the design goals of the equipment is crucial for the success of the project. Here, the desired performance and functions of the equipment are outlined, including targets for production capacity, precision, and the level of automation. Quantifying these goals helps set a clear development path, allowing the project to proceed without deviation.
・Production Capacity
Production capacity is the numerical goal indicating how much the equipment can process. For example, specifying how many products the machine can process per hour or how many batches can be produced in a day's working hours.
This goal should be set considering how much improvement is expected compared to existing production levels. Typically, aiming for double the production capacity of manual operations or ensuring adequate production capacity with room for growth is common.
・Precision Goals
Automation equipment must achieve high precision to ensure consistent product quality. Precision goals include aspects such as dimensional accuracy, machining precision, and positioning accuracy.
For instance, when designing equipment that can process or position parts with an accuracy of ±0.1mm, the selection of the control mechanisms and sensors becomes critical. Achieving this precision goal will lead to stabilized product quality and reduced defects.
・Level of Automation
The level of automation indicates how much manual labor is replaced by automated processes. Sometimes full automation is required, while in other cases, semi-automation, where manual labor complements the system, may be appropriate.
For example, it is important to decide whether to automate the entire process from material input to machining, inspection, and shipping, or to leave certain tasks to human workers. When setting the level of automation, it is essential to consider the balance with costs and development time, aiming for the minimal level of automation needed.
・Other Goals
In addition to these, other factors such as operating costs, energy consumption, and installation space must also be considered. For instance, designing energy-efficient equipment can contribute to lower running costs and reduced environmental impact. Additionally, compact designs that fit the factory layout are often critical considerations.
These goals should be customized to the needs of the site, and close communication with field staff is essential.
Constraints (It’s tough when there are so many issues...)
When designing automation equipment, it’s essential to consider not only the ideal goals but also the practical constraints. Ignoring these constraints could lead to the project stalling midway. Common constraints include investment costs, development timelines, and factory building or utility regulations.
・Investment Costs
Introducing new equipment often requires significant investment. Investment costs include not only the cost of the machinery itself but also design, installation, and, in some cases, factory renovations. Therefore, careful cost estimation is necessary.
For example, if the budget is limited, considering phased implementation can be effective. By automating only part of the process first and expanding as effects are confirmed, risks can be minimized, and costs can be controlled. Moreover, it’s important to design equipment with only the necessary functions to balance cost and functionality.
・Development Timeline
Designing and introducing automation equipment takes time. The development timeline is often strictly set according to the manufacturing project schedule and market needs, with short lead times frequently demanded.
To meet deadlines, unnecessary revisions or redesigns during the design phase must be minimized. Therefore, clearly defining the design goals and constraints early on is crucial. Additionally, proper project management is essential to ensure smooth progress from design to manufacturing and trial runs.
・Factory Building and Utility Regulations
The constraints of the factory space and existing utilities (electricity, air conditioning, drainage, etc.) cannot be ignored. New equipment will need to fit within the available space in the factory, and in some cases, a layout change may need to be considered. This issue is particularly prominent for large-scale equipment or installations in specialized environments such as clean rooms.
Furthermore, if the equipment requires utilities like power, compressed air, or cooling water, the design must ensure it does not exceed the existing capacity. These utilities are directly related to the operational costs of the factory, so efficient usage must be considered in the design. It’s essential to confirm whether the new equipment can integrate smoothly with the existing infrastructure during the planning stage.
How to Consider Equipment Configuration
In the conceptual design of automation equipment, deciding how the equipment will be configured is a critical point. You need to consider how the equipment will operate, how materials will be fed, and how they will be machined or assembled. Here, we’ll explore four key factors in determining equipment configuration: operation breakdown, feeding methods, material supply methods, and machining methods.
■ Breaking Down Operations
When considering equipment operations, it’s important to break down the entire process into smaller steps. If a single machine handles multiple processes, it’s necessary to organize each step as an independent operation and consider how they work together.
For example, in an assembly process, there are several steps: "material supply," "positioning," "assembly," "inspection," and "output." Clearly breaking down these steps and ensuring each operation proceeds efficiently without waste will help maximize the overall efficiency of the equipment. Additionally, the speed and timing of each operation are critical as they impact the overall cycle time. Therefore, it’s essential to design with consideration for balance between operations.
■ Feeding Methods
The feeding method refers to how materials or products move within the equipment. Two main methods are commonly used:
- Intermittent feeding: This method moves materials or products in a stop-and-go fashion at set intervals. It’s typically used when materials must stop at a processing or assembly point before moving on to the next stage. This method is effective in processes that require high precision or when synchronization across multiple stages is needed.
- Continuous feeding: This method moves materials without stopping, at a constant speed. In high-throughput production lines, continuous feeding is often adopted to efficiently handle large volumes of products.
When choosing a feeding method, it’s necessary to consider the size, weight, and shape of the products, as well as the required precision and cycle time at each stage. Intermittent feeding is suitable for precise positioning, while continuous feeding is ideal for handling large volumes at high speed.
■ Material Supply Methods
Material supply methods refer to how the materials used in the equipment are supplied. The following are some common methods:
- Bulk supply: In this method, materials are supplied in bulk (in a loose, disorganized state), and then aligned and fed into the machine in the correct orientation. It is common to use feeders (such as bowl feeders) for alignment. While bulk supply is a cost-effective and efficient method, the alignment process can be complex.
- Pallet supply: In this method, materials are supplied pre-aligned on pallets or trays. Since the materials are already aligned, the supply speed is faster, and no alignment process is needed. However, preparing the materials in an aligned state before supply requires extra effort and cost.
When choosing a supply method, it is essential to consider the shape, size, supply speed, and cost of the materials, and select the most appropriate method.
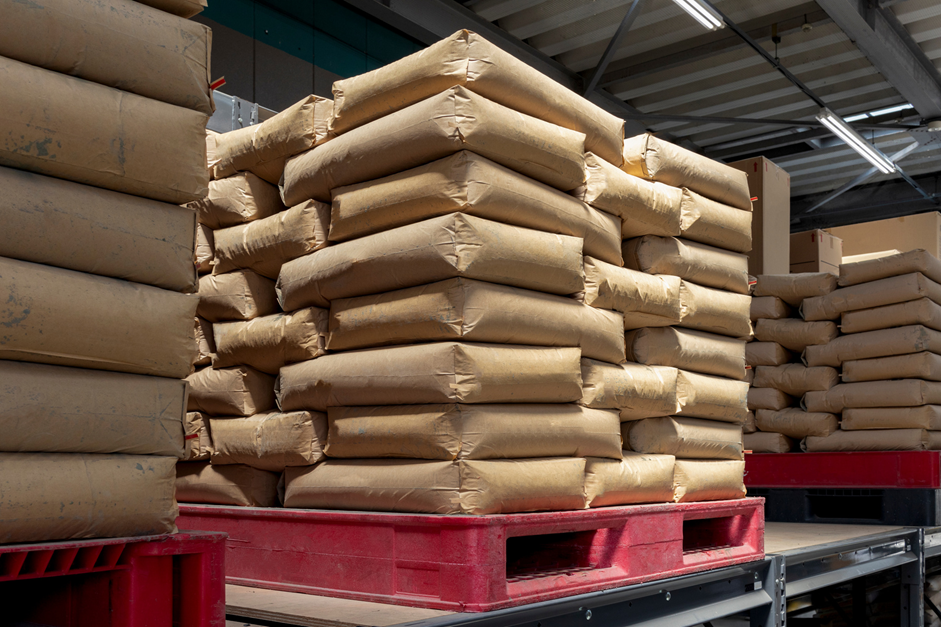
■ Machining Methods
How materials or products are machined inside the equipment is another key aspect of the design. Machining methods include cutting, welding, assembly, inspection, and other processes. Each machining method requires appropriate equipment based on its characteristics and precision requirements.
For example, in assembly processes, material handling and positioning are critical, requiring precision robotic arms or positioning devices. For processes like welding or bonding, temperature control and pressure management during machining have a significant impact on precision.
Key Considerations in Mechanism Design
In designing automation equipment, selecting and designing the mechanism is a critical step. The choice of the optimal mechanism affects the efficiency, stability, and maintainability of the equipment. This chapter explains key considerations such as optimal mechanism selection, handling and positioning methods, material supply methods, maintenance readiness, and environmental considerations.
■ Optimal Mechanism Selection
Choosing the optimal mechanism requires balancing the efficiency, precision, durability, and cost of the operations while considering the design goals and constraints.
Here are some points to consider:
- Aim for simplicity: Complex mechanisms increase costs and the risk of failure. Therefore, the design should aim to achieve the desired functionality with the minimal necessary mechanism. A simple yet effective mechanism also contributes to easier maintenance and repairs.
- Incorporate redundancy: To minimize downtime in production lines, it’s important to incorporate redundancy in critical areas. For instance, providing backup motors or sensors in critical components can reduce the risk of equipment stoppages.
- Choose high-precision mechanisms: For tasks requiring precise movements, selecting appropriate guide rails, ball screws, and linear guides is crucial. This helps improve positioning accuracy, movement smoothness, and overall reliability of the equipment.
■ Handling and Positioning Methods
Handling and positioning of materials and products are crucial elements for the success of automation equipment. This includes moving, rotating, lifting, conveying, and precisely positioning materials.
- Robotic arms: Robotic arms are often used for advanced handling, especially when complex movements or handling delicate products are required. Robotic arms come in various types, such as articulated or SCARA, and must be selected according to the application.
- Positioning devices: For high-precision positioning, systems that combine encoders and sensors are used. This enables positioning accuracy down to microns, playing an important role in precision machining or assembly processes.
■ Material Supply Methods
Material supply methods greatly affect the operational efficiency of the equipment. If the supply is not smooth, it can reduce the overall performance of the equipment, negatively affecting productivity.
- Bowl feeders: Bowl feeders are commonly used for aligning and supplying small parts. Bulk materials are aligned using vibration or gravity and fed into the next stage, making it suitable for mass supply.
- Linear feeders: Linear feeders, which supply materials in a straight motion, are effective for conveying materials in a specific direction. They are suitable for continuous and precise supply, making them ideal for processes requiring a steady flow of products.
■ Maintenance Readiness
For long-term operation of automation equipment, maintainability is an important design element. Considering ease of maintenance during the design phase can minimize downtime and extend the lifespan of the equipment.
- Ensure accessibility: It’s crucial to design equipment so that critical components and mechanisms are easily accessible during maintenance. Ensuring there are openings and maintenance spaces to quickly replace or repair parts contributes to efficient operation.
- Incorporate preventive maintenance: By using sensors and monitoring systems to monitor the equipment's status in real-time, it’s possible to detect signs of failure and address them before they occur. Incorporating this preventive maintenance system can prevent unplanned downtime.
■ Environmental Considerations
In recent years, environmental considerations have become increasingly important in automation equipment design. Reducing environmental impact and improving energy efficiency are important corporate social responsibility (CSR) issues.
- Energy-saving design: It is essential to adopt energy-efficient motors and control systems to reduce power consumption. Additionally, designing equipment to minimize power consumption in standby mode can lead to long-term cost savings and reduce environmental impact.
- Compliance with environmental regulations: Noise levels, emissions, and the use of chemicals in the working environment must also comply with local regulations. Equipment designed for use in cleanrooms must meet strict standards.
Case Study: Implementation of Conceptual Design
When progressing with the conceptual design of automation equipment, referring to actual project examples helps clarify the specific steps that should be taken. Here, we introduce a case study of an automation equipment project in a production line and explain the process step by step.
■ Case Study: Conceptual Design of a Precision Parts Assembly System
This case study focuses on a project to design equipment for automating the assembly of precision parts. In manual assembly, variation in quality and production speed limitations were significant issues. To improve both quality and productivity, the equipment was designed through the following steps:
1. Clarifying Design Objectives and Goals
First, the purpose and goals of introducing the equipment were set. This project focused on the following points:
- Increasing production capacity: Manual assembly was limited to 100 units per hour, but the goal was to double this to 200 units with the automated system.
- Ensuring consistent quality: Human labor caused slight misalignments during assembly. The goal was to achieve assembly precision within ±0.05mm using the equipment.
- Reducing worker burden: Another goal was to reduce the repetitive workload on workers, allowing them to focus more on monitoring and quality control.
2. Confirming Constraints
Next, the project constraints were reviewed.
- Investment costs: Due to budget constraints, the decision was made to use existing technologies and modules as much as possible.
- Development timeline: The schedule was tight, requiring the system to be operational within six months. To meet this deadline, a phased automation approach (gradually automating parts of the process) was planned.
- Factory space constraints: Space next to the existing production line was limited, so a compact design was necessary.
3. Equipment Configuration Considerations
To decide on the basic configuration of the equipment, operations were broken down, and the optimal mechanisms and methods were considered for each stage.
- Breaking down operations: The assembly process was divided into "material supply," "positioning," "assembly," "inspection," and "output," and the appropriate mechanisms for each stage were selected.
- Feeding method: Since continuous production was necessary, linear feeders were used for material supply and conveyance, delivering materials at precise intervals.
- Handling and positioning: A multi-jointed robotic arm was employed for assembly, with a high-precision positioning system utilizing encoders.
4. Turning Challenges into Opportunities
During the design process, several issues arose, but they were resolved by changing the approach.
- Assembly precision issues: In the initial prototype phase, the assembly precision did not meet the target. However, by adjusting the placement of positioning sensors and fine-tuning the control software, the precision was improved.
- Cost constraints: Instead of using expensive specialized modules, existing robotic arms and off-the-shelf components were utilized to reduce costs.
5. Maintenance and Environmental Considerations
With long-term operation in mind, attention was paid to ease of maintenance.
- Maintenance: Access panels were installed in key areas of the equipment, and sensors for preventive maintenance were added. This allowed the equipment's status to be monitored continuously, enabling maintenance before issues arose.
- Environmental considerations: To reduce power consumption, energy-saving designs were implemented, and noise levels were minimized by installing soundproof covers.
6. Results
Ultimately, the equipment achieved the target production capacity and precision, reducing the burden on workers. Additionally, by adopting a phased implementation strategy, the equipment was operational in a short period of time.
Strategies to Avoid Oversights in Conceptual Design
In conceptual design for automation equipment, missing critical elements during the design phase can lead to major revisions later or cause the equipment to fall short of expectations. To avoid such oversights, it is essential to consider all factors in advance and establish a comprehensive plan. This chapter introduces specific strategies to avoid oversights in the design process.
■ Identifying Key Functions
Before starting the design, it is important to clearly define all necessary functions for the equipment. By breaking down the entire work process into smaller tasks and clarifying the requirements for each stage, all necessary functions can be comprehensively identified.
- Organizing functional requirements: Start by listing the goals and functions the equipment must achieve and prioritize them. Clearly defining functional requirements helps ensure that critical elements are not missed during the design phase. For example, clearly defining the operations and conditions required at each step, such as "material supply," "machining," "conveying," and "inspection," is crucial.
-
Considering the user interface: Designing an intuitive user interface enhances the convenience
for on-site workers. Control panels and touch screens should also be considered as part of the equipment's functionality.
■ Cost Considerations
Neglecting cost considerations during the conceptual phase can result in budget overruns or additional investments after development. Proper cost management involves thoroughly estimating costs early on and aiming for a cost-effective design.
- Budget management: The total cost of implementing the equipment includes not only manufacturing costs but also operating and maintenance costs. For example, even if initial costs are high, selecting an energy-efficient design can reduce operating costs, leading to long-term savings.
- Exploring alternatives: When expensive components or modules are required, it is worth considering whether they can be replaced with more affordable alternatives. In projects with limited budgets, it's important not to overlook alternative technologies to reduce costs.
■ Safety Measures
Ensuring safety is one of the top priorities in the design of automation equipment. It is essential to identify potential risks early in the process and incorporate safety measures to prevent accidents or issues during operation.
- Risk assessment: Conduct a risk assessment during the design phase to identify potential hazards during operation and implement necessary measures. For example, installing safety covers on moving parts or positioning emergency stop buttons in accessible locations can help prevent accidents. Safety logic that automatically stops the equipment in case of abnormalities should also be incorporated into the control system.
- Compliance with safety standards: The equipment design should comply with international safety standards and local regulations. Designing the equipment to meet standards like ISO or CE marks will enhance the product's reliability and reduce the risk of liability in the event of an accident.